What is a stamper battery?
Shirley commented on my last post asking what a stamper battery is. I must admit to getting a bit carried away here, but the question prompted some thought and I have a project coming up that has to have an explanation written, so here is the first draft:
A stamper battery [a row of rock crushing stampers] represents one of many techniques to separate gold from earth and rock. The ratio of gold to dirt/rock is what determines the financial viability of a gold mining operation. Machinery is inevitably employed and has a capital cost as well as a very high maintenance cost: water is usually involved too and steel machinery is not best lubricated by water especially as it has rock particles in suspension in a gold mining operation [I'll leave it to the reader's imagination to ponder the downstream effects on water and river quality!].
There are many areas or land in my homeland of Central Otago where what is called the peneplain is exposed by weathering, maybe aided by glaciers having stripped away substantial debris earlier, and also faulting crinkling the surface of the earth thus exposing edges where weathering can occur faster. Anyway you don't have to rush off to the link below - just to know that rocks in keeping with a high percentage of gold are on the surface or can be mined/transported easily to a battery.
http://en.wikipedia.org/wiki/Peneplain
These rocks will typically be much heavier than our greywacke and shists, and they've once been part of layers of sediment cooked with pressure under extreme weight and silica has been forced all about. Quartz is also evident, along with "petrified wood".
Stampers have to be constructed out of material tougher than silica impregnated rocks and crush same, then water is used to transport the crushings through a complicated refining process that leads to a water, gold and rock crushings mix [slurry].
Water was often also brought to the battery to power it, via races constructed with great effort out of creeks and around hill sides slowly loosing height to the site of the battery. The levels were calculated by using old gin bottles almost full of water [hence the phrase "spirit levels" perhaps].
When at the battery the water flowed onto a wheel thus suppling motion to a shaft on which a number of cams [all offset to ensure balance] would lift and then drop [stamp] very heavy cylinders of steel onto the rocks. The noise is awesome [some enthusiasts have restored one on the West Coast and I've been fortunate to see it running briefly]
This photo shows the curved cams that raise and drop the shafts that have the huge weights at the bottom:
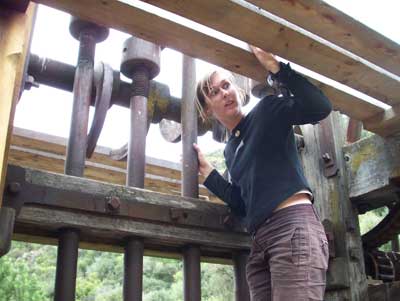
The last photo below shows the wheels on the left that turn the shaft. At the level of Camille's waist you can see the weights [stampers], and the photo is taken looking towards the exit side of the battery - in other words where it's taken from would have had quite sophisticated sluices with water washing the crushings along them, first over steel with large holes/gratings so rocks could be stopped while the fines dropped through, eventually to be caught on carpet in more chutes [water still used], and eventually separated out by the use of mercury and heat, and made into ingots

For me two factors in these operations astound me: how did they get the components on-site? And how did they live [or not live] in the winters!? Keep in mind that it is springtime when water is most abundant - this must surely mean working hard and long hours to have the material ready. Especially in some situations where, the water being temporarily frozen would aid the mining!
A stamper battery [a row of rock crushing stampers] represents one of many techniques to separate gold from earth and rock. The ratio of gold to dirt/rock is what determines the financial viability of a gold mining operation. Machinery is inevitably employed and has a capital cost as well as a very high maintenance cost: water is usually involved too and steel machinery is not best lubricated by water especially as it has rock particles in suspension in a gold mining operation [I'll leave it to the reader's imagination to ponder the downstream effects on water and river quality!].
There are many areas or land in my homeland of Central Otago where what is called the peneplain is exposed by weathering, maybe aided by glaciers having stripped away substantial debris earlier, and also faulting crinkling the surface of the earth thus exposing edges where weathering can occur faster. Anyway you don't have to rush off to the link below - just to know that rocks in keeping with a high percentage of gold are on the surface or can be mined/transported easily to a battery.
http://en.wikipedia.org/wiki/Peneplain
These rocks will typically be much heavier than our greywacke and shists, and they've once been part of layers of sediment cooked with pressure under extreme weight and silica has been forced all about. Quartz is also evident, along with "petrified wood".
Stampers have to be constructed out of material tougher than silica impregnated rocks and crush same, then water is used to transport the crushings through a complicated refining process that leads to a water, gold and rock crushings mix [slurry].
Water was often also brought to the battery to power it, via races constructed with great effort out of creeks and around hill sides slowly loosing height to the site of the battery. The levels were calculated by using old gin bottles almost full of water [hence the phrase "spirit levels" perhaps].
When at the battery the water flowed onto a wheel thus suppling motion to a shaft on which a number of cams [all offset to ensure balance] would lift and then drop [stamp] very heavy cylinders of steel onto the rocks. The noise is awesome [some enthusiasts have restored one on the West Coast and I've been fortunate to see it running briefly]
This photo shows the curved cams that raise and drop the shafts that have the huge weights at the bottom:
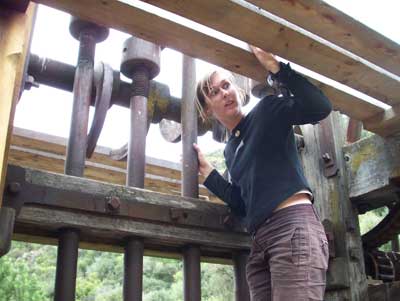
The last photo below shows the wheels on the left that turn the shaft. At the level of Camille's waist you can see the weights [stampers], and the photo is taken looking towards the exit side of the battery - in other words where it's taken from would have had quite sophisticated sluices with water washing the crushings along them, first over steel with large holes/gratings so rocks could be stopped while the fines dropped through, eventually to be caught on carpet in more chutes [water still used], and eventually separated out by the use of mercury and heat, and made into ingots

For me two factors in these operations astound me: how did they get the components on-site? And how did they live [or not live] in the winters!? Keep in mind that it is springtime when water is most abundant - this must surely mean working hard and long hours to have the material ready. Especially in some situations where, the water being temporarily frozen would aid the mining!
1 Comments:
OK, now I know!
Post a Comment
Subscribe to Post Comments [Atom]
<< Home